60%
reduced investment costs
Using this technology for innovative new products does not only enable you to increase your production capacities but also to reduce the facility costs to almost the half.
20%
lower manufacturing costs
Better quality, the production costs being lower - optimized processes and production methods enable you to increase the economic efficiency of your innovation and company.
40%
higher
productiveness
The revolutionary EXJECTION Endless Technology makes it possible to produce much more components within the time unit than at the conventional injection moulding process.
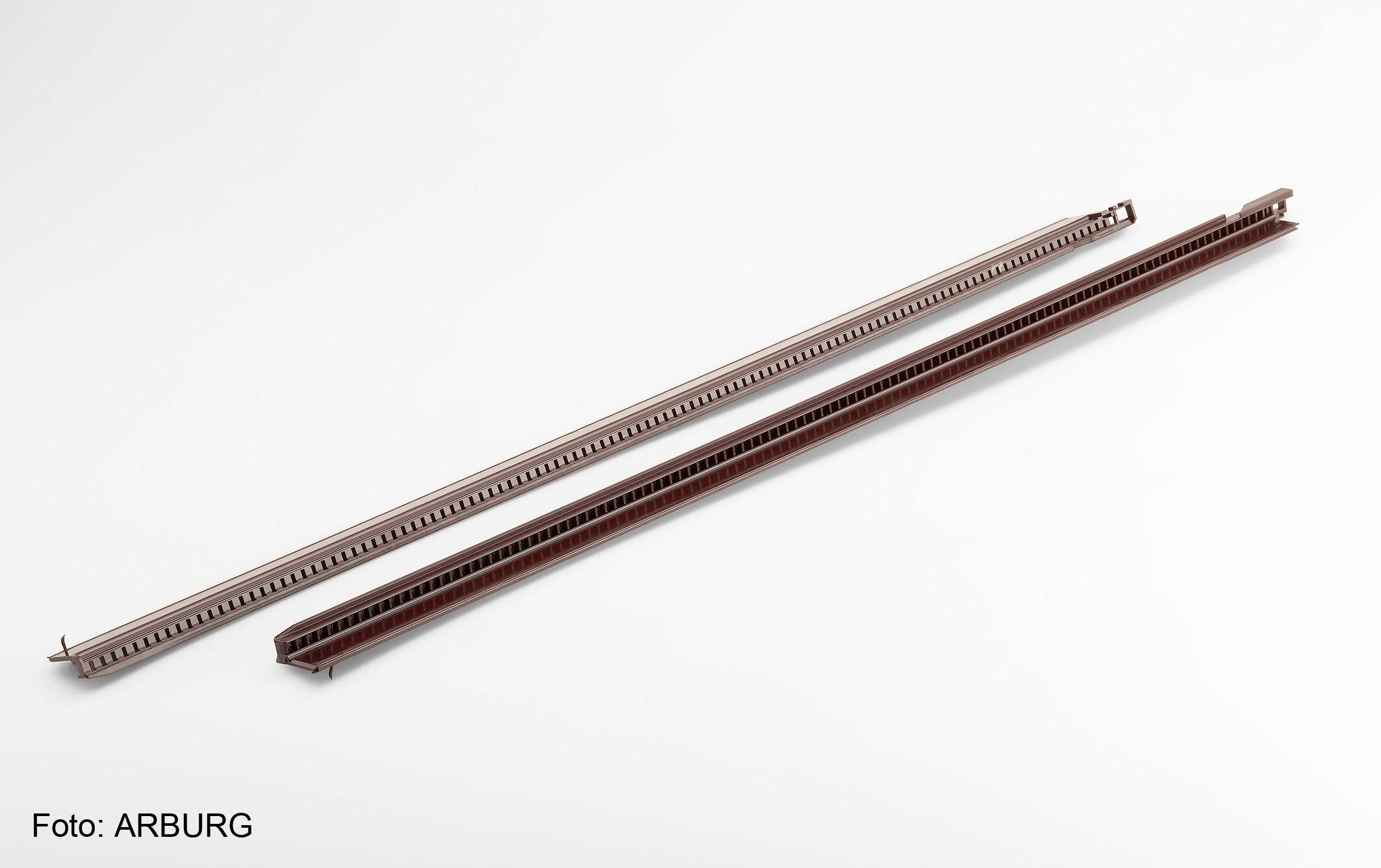
EXJECTION facilities that have already been implemented make it possible to manufacture very long components at small closing forces. As a comparison with the machines that are otherwise necessary for injection moulding of long components and have closing forces that are much higher, energy consumption can be reduced by approx. 60 %.As far as the investment volume is concerned, the average saving potential offered by EXJECTION amounts to about 40 % as compared to conventional injection moulding. This means that the the production costs will be made to be 20% lower by the new process.
The opportunities offered by continuous production using the EXJECTION endless process go far beyond this potential, which is already known. For the first time, it becomes possible to realize production of components on one injection moulding machine without the period of dry operation of the machine having an adverse impact on the overall cycle. Continuous production using endless technology no longer knows any unproductive opening and closing of the mould. It will only be necessary to invest the time that is necessary to fill the cavity. Thanks to this, energy efficiency of your company and production can be improved even more. This will have a positive effect on economic efficiency as a whole.
Trim Strip Example
The example "Trim Strip" can refute the following comparison:
Main dimensions: 1.440 mm x 30 mm x 19 mm (L x W x H)
Wall thickness: von 1,5 mm
Weight: 77 g
Material: ABS
Number of cavities: 1
Clamp force demand:
6500 kN with moulding -> 500 kN with EXJECTION
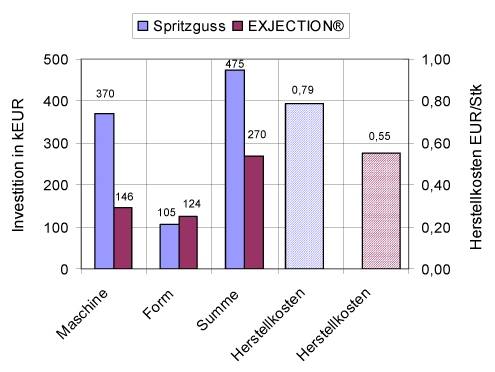
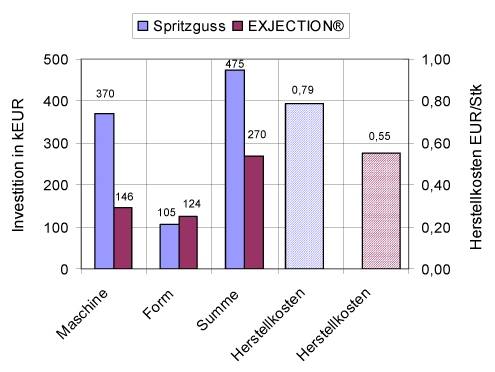
Low flowing distances
more freedom of design enabled by EXJECTION
Minimum needs for closing forces
EXJECTION expands horizons
Avoidance of Weld Lines
EXJECTION will captivate you as well.
Gentle processing of the molten mass
in-mould decoration using EXJECTION
High-quality surfaces and decorations
shining prospects offered by EXJECTION
